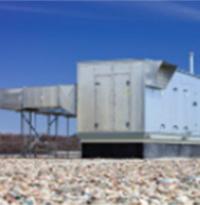
How Budget Managers and Facility Executives can take Savings Seriously
Maintaining a building’s HVAC system should not be done off of the principle “When it’s broke we’ll fix it.” It’s the most costly way to operate and yet in spite of the case studies proving this, almost all facilities still maintain their systems in this reactive manner.
In typical commercial buildings, HVAC systems are responsible for 40 percent of total energy use. It would seem that ensuring preventive measures would take precedence in the budget because of this. However, there are understandable reasons why this isn’t the case.
Common Causes for HVAC Budget Shortfalls
- Lack of Resources – This is the most common reason for not performing routine and preventive maintenance of HVAC equipment. To many of those who control the budget, the approach is to think of maintenance as overhead cost and do everything possible to reduce that cost, which includes preventive measures.
- Out of Sight Out of Mind – HVAC components are not as visible as other facility materials, like light fixtures or flooring. This makes things easy to ignore until something goes wrong. Then, it’s too late for preventive measures.
- Proper Communication – Facility Executives can have difficulty receiving the necessary budget support because of inadequate explanation of the issue. A case needs to be made to the budget manager about the consequences of ignoring HVAC preventive steps, especially when these don’t yet involve broken components. Demonstrating how dollars and cents can be saved in the long run is essential.
HVAC Documentation
The best way to show that preventive measures lead to long term savings relies on documentation.
There are benefits that can be documented easily, making clear that preventive steps provide a greater rate of return than the outcome of other departments whose projects are competing for the same budget dollars.
One such benefit is how HVAC maintenance effects energy efficiency. Facilities in which proper HVAC maintenance is completed will use 15 to 20 percent less energy than those where systems are left uncared for.
An example of this is the central building chiller, which typically causes the largest use of electricity in a building. Keeping one operating at a high level of efficiency takes a range of daily, weekly, monthly and yearly procedures. To let this lapse, would be to compromise savings on energy use.
If one were to implement the use of a chiller operating log, and work with an HVAC specialist to help interpret the log data, an operating efficiency curve could be drafted. This could then be compared to how the chiller would run if all the maintenance was handled at its scheduled time. The difference between the two could be translated into energy and cost savings.
Common Sense Cost Saving
The fact is, companies that implement planned and predictive maintenance protocols show huge decreases in maintenance costs.
These factors alone reduce up to 50 percent of the costs to companies that use only reactive measures.
- Reduced energy use
- Decrease of interruptions to a building’s operations.
- Extended life for HVAC equipment
- Lower frequency of system downtime.
So if it’s time to look at how your company’s facility can start digging out of high energy use, increase the life of your HVAC equipment and get on track for long term savings, contact AAA Able Air Conditioning and Appliance Inc.
AAA Able Air Conditioning and Appliance Inc. has been serving the South Florida business community for over thirty years. We know when times are good, budget issues are less of a concern than creative growth, and when times are lean, the budget takes a front seat in every decision. We work with customers to get the most out of their HVAC infrastructure and help establish comprehensive plans for continued energy savings. We do regular inspections, testing and maintenance. Contact us today and lets get started.